Taking new technologies and overlaying them on today’s practices isn’t enough. Companies must undergo a transformation, a ‘digital transformation’, in order to fully reap the rewards.
The adoption of the dynamo, a disruptive technology of the 19th century seen through the eyes of a victorian engineer, provides an insightful analogy.
Digital Transformation is described by Wikipedia as, “the adoption of digital technology to transform services or businesses.”, but it is hard to think of any business or industry that isn’t already using digital technology in some form or other. Whether that be the day-to-day applications that employees use: databases, online chat, mobile apps, social media, the aspiration to become paperless.
And so when we talk of Digital Transformation, we can wonder how many efficiencies are there left to be gained? If a company has already embraced newer technologies such as blockchain, IoT, AI and big data, surely they are ahead of the curve? Aren’t they already the bold pioneers of new technology? And for companies that are not primarily technology companies, does the term Digital Transformation even apply to them?
Before we attempt to answer this, we need to recognise that digital technologies evolve at an incredibly fast pace, and their affect can be transformative. The world is arguably a different place today than it was even 5 years ago because of disruptive technologies like the cloud and the web. Cloud, for instance, has brought us scalability, cost savings, reliability, mobility, easier disaster recovery – to name but a few. So if your company has already ‘moved to the cloud’, have all the benefits now been realised?
The reality is, Digital Transformation is much more than simply using new technologies; businesses also need to transform their processes and practices in light of what these digital technologies now make possible.
History can teach us this as well. Tim Harford’s ‘50 things that made the modern economy’ BBC episode on the dynamo looks at the adoption of a 19th century ‘disruptive technology’.
Before the invention of the dynamo, factories were powered by steam engines. The intense heat from the coal powered steam engine drove a central steel shaft that would run right through the factory. Attached to this rotating shaft would be multiple subsidiary shafts. A magnificent tapestry of belts, cogs and pulleys would all work together to harness the power of the central rotating shaft.
To stand in an early 19th century factory would be an incredible experience; the deafening repetitive noises, the dust in the air, the smell of the coal fire. Belts would travel between different stories of the factory through holes in the floors and ceilings. The speed of the whole factory, the repetitive manual tasks: all driven by the speed of the steam engine.
When the electric dynamo was first introduced to the factory, there were some obvious benefits. The far-sighted electrical engineer could visualise all factories leaving their steam engines for the electric powered dynamo. The dependency on the central driving shaft would be alleviated, and parts of the factory could work independently of each other by using their own motors or dynamos. No longer would the coal fires have to be lit if only one of the departments needed to work. If one part of the production process needed upgrading or servicing, no longer did the whole factory need to down tools whilst this took place. The dynamo would mitigate against the foibles of ‘belt slippage’ and its ensuing quality problems.
The installation of variable power D.C motors would enable a workstation to run at a speed suitable to the worker or appliance. No longer would the air and surfaces be full of the grease used by thousands of drip oilers to oil the shafts. Cleaner and safer electricity could facilitate a working environment where workers were less likely to be maimed or killed by getting caught up in the belts and pulleys that distributed power around the factory.
What the episode goes on to discuss is that the factory owners who were early to embrace the electric dynamos did not achieve the productivity gains they would have hoped for. It took about 50 years for the dynamo to be fully embraced and the productivity gains over using a steam engine to be fully realised.
Of course, over time there were many factors that affected this; the price and reliability of the new dynamos, the availability of mains electricity, the price of workers and the availability of skilled workers. But the main change that really gave the dynamo its return on investment, and one that took around 50 years, was when the factory owners figured out how to transform their business around the dynamo.
The factories owners couldn’t just change their steam engines to a dynamo, the factory owners had to change everything. Old factories were based around the logic of the production line. The factories were old, dark and dense, packed around the shaft. New factories could be based around the logic of the production line, and could spread out on a single floor building with wings and windows to bring in natural light and air. New factory structures were cheaper to build as they did not need to be durable enough to stand the powerful forces exerted by the rotating shafts. Work became less about quantity and more about quality. Highly trained workers could use the autonomy that electricity gave them, to further streamline processes and increase their quality control. Workers could set their own pace, using machines only when required in a much safer and cleaner environment.
The highly skilled engineers of the day were exposed to lots of different factories and practices across the country. They understood what had worked and what didn’t. They understood it wasn’t just the dynamo that needed the change, but a multitude of other things as well. Through consultation and implementation with skilled engineers, factory owners were able to free their businesses from the huge burden of ‘trial and error’ process that they would have inevitably gone through without the skilled engineers’ wisdom.
There are obviously many differences between the implementation of the electric dynamo and digital technologies; the technical problems of designing efficient interfaces for humans and computers are enormously more subtle and complex than those of the interactions between man and machine. But this history lesson does provide a fresh perspective when looking at how to harness the benefits of a new technology. Throughout history the overlaying of one technical solution is not unusual during historical transitions from one technological paradigm to another. The factory owners who were able to harness the benefits the most effectively were the ones who were able to think through the implications of a world where everything needed to adapt to a new technology. The factory owners who were brave and willing to constantly adapt were the ones who reaped the most rewards.
The enthusiasm, vision and perceived benefits are usually abundant in these situations. The implementation is the biggest hurdle. The real challenge is to analyse how everything else needs to change in order to create a successful Digital Transformation. Allowing the mere passage of time to create occasions to radically redesign a company is going to be a lot slower than doing it now. Let’s be under no illusion: Digital Transformation is difficult. If not done right, it can involve a huge amount of time, cost, and trial and error, with very little benefit to show for it. The dynamo analogy demonstrates this perfectly; it’s not good enough just to ‘move a VM to the cloud’, it’s not enough to just ‘use’ new tech; you only reap the benefits when you do it the right way and for the right reasons. You need to be motivated by ‘solving a problem’, not just ‘keeping up’, and this is the hard thing about Digital Transformation – doing it efficiently, effectively, and for the right reasons, so that you save costs and achieve better outcomes.
Hexiosec have seen the benefits gained when Digital Transformation is done well, and how successful and cost effective it can be. Companies should look at whether their processes and cultures could change to get the most out of their digital technologies. Digital Transformation, along with Cyber Security, can often be more about transforming processes and culture than about technological implementation, and all companies need to keep transforming no matter what stage of digital technology adoption they are at.
References
https://www.bbc.co.uk/programmes/p057xsl0 - 50 Things That Made the Modern Economy
The Dynamo and the Computer: An Historical Perspective On the Modern Productivity Paradox, Paul A. David, 1990
Image: https://www.pexels.com/@pixabay
Related Posts
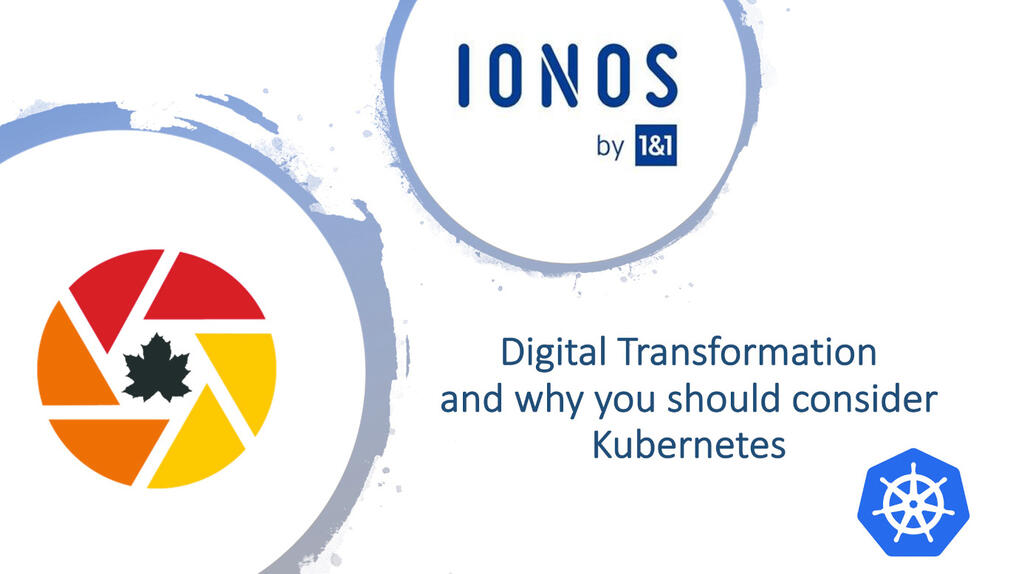
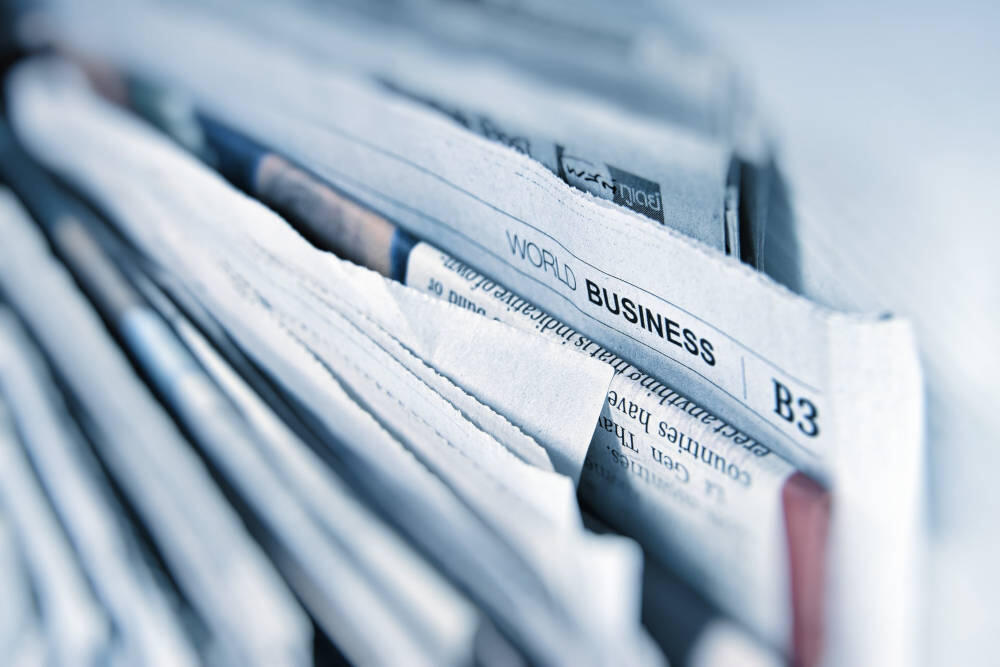
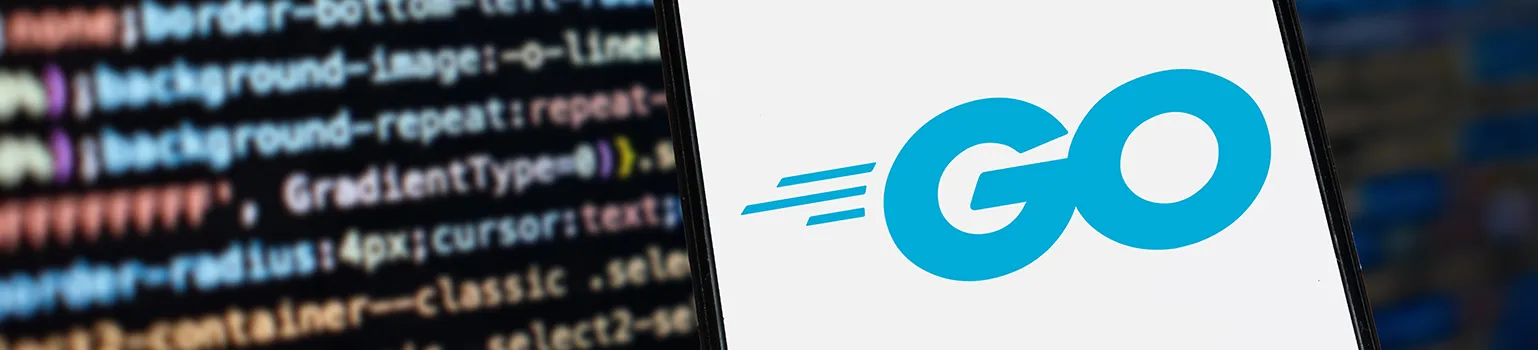